In the late 1970s, DARPA initiated a program with Lockheed Space Systems Division to develop the technology of welding aluminum-lithium alloys, which would combine high stiffness with low density and therefore lower weight. At the time, no one understood how to prepare these materials for welding and how to control impurities in the metals and welding process. Such control would be critical for producing materials repeatedly with predictable behavior and performance.
Within 18 months, metallurgists at Lockheed had developed the welding techniques for the 80/90 Al/Li alloy and applied it to the construction of space hardware. One of the most impressive structures made from this material was the Titan missile payload adapter, which was 14 feet in diameter and 17 feet high and fabricated from 3" thick metal plate. By using this alloy, a 10% weight saving was achieved compared to the prior incarnation of that rocket components. The weight savings translated into millions of dollars at cost savings when it came to delivering hardware to obit. This material system made it into classified DoD applications as well. Lockheed scaled the process up to 400,000 lb/year of Al-Li alloys for the next four years.
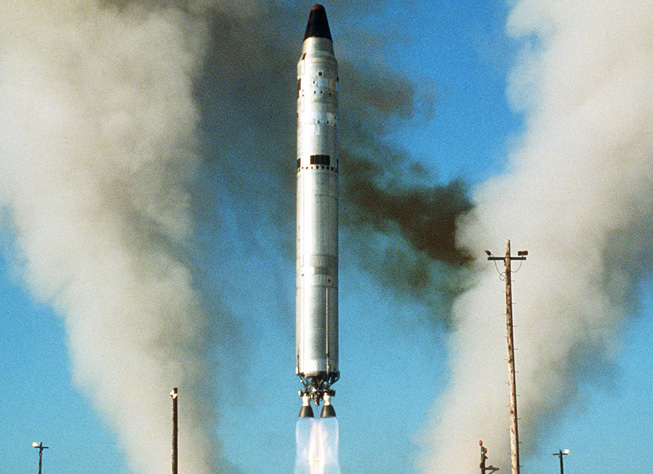